Testing and Engineering Analysis
Container Level Detection
Level detection was a concept added later to the PreSpice which implements an array of photo transistors and LED's. The test was to see how accurate 4 photo transistors were at different levels of the container being filled. The plot shows how each photo transistor activated with time as the spice level got lower and lower. This confirmed that the accuracy of the level detection is roughly equivalent to the number of activated photo transistors.

Carousel Stress Analysis
Due to the carousel position needing to be very precise in order for each container to align with the end-effector correctly, the carousel needed to be thick enough to avoid any significant bending. if it was under the maximum force. Using a 1/4in thick piece of acrylic, a Solidworks stress analysis was done to show that the maximum displacement of .32mm will occur at the positions shown in red in the photo on the right, well within the tolerance limit for the end-effector to mesh.
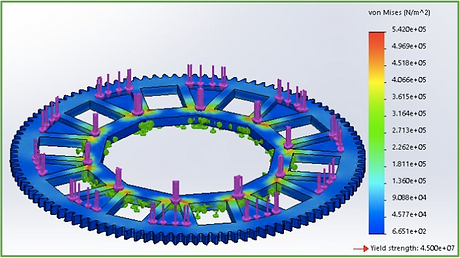
Carousel Motor Selection
The motor that rotates the carousel is a stepper motor paired with a gear ratio of 111:15. To properly determine the size of the motor required for the carousel to rotate, a torque analysis was done. The analysis consisted of using SolidWorks to calculate the total inertia of the system when each container was full of spice. Approximations with the angular velocity and acceleration were also used to calculate the desired holding torque for the carousel. Using a safety factor of 4, the minimum holding torque required was 13.6Ncm. The carousel motor selected was a Nema 17 stepper motor with a maximum holding torque of 59 Ncm and a max angular velocity of 300rpm, well within the limit required for the carousel to operate correctly.

End-Effector Stress Analysis
The end effector pieces were going to experience a maximum torque of 59Ncm assuming the max amount of torque would be applied to the end. Assuming the end effector material is resin, a Solidworks stress analysis was performed showing a max displacement of each tooth to be .4mm which the resin can easily flex to without fracturing.

Linear Actuator Motor Selection
The PreSpice implements a linear actuator system to linearly couple two end-effectors together. The linear actuator moves a motor that couples an end-effector to a container dispensing wheel. The motor system designed for the linear actuation incorporates a rack and pinion system paired with two stepper motors for precise control of its position. A complete torque analysis was done to determine the minimum torque required for the two stepper motors used. With approximations made on speeds and accelerations, along with using a safety factor of 4, the minimum torque for each stepper motor came out to be 2.7Ncm. With the size of the steppers being a limiting factor, the stepper motors selected were the 28BYJ-48-5V steppers. These are small stepper motors that have a max holding torque of 3.4Ncm.
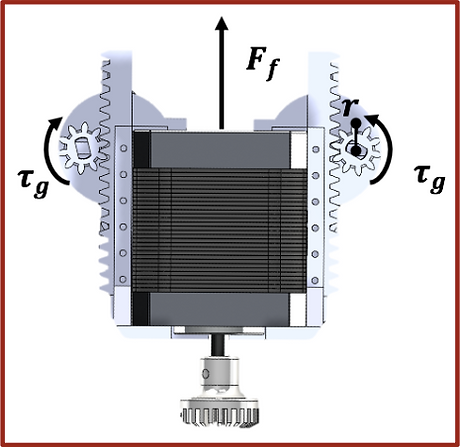